오늘 품질에 대해 생각을 다시 해 봤다. PDCA Cycle과 PDCD Cycle을 항상 알고는 있었지만, 과연 업무를 수행함에 있어 Cycle 을 완전하게 돌려보고 적용해 본적이 몇번이나 있던지 ? 많은 방법들이 있고 개선안들도 있지만 .... 음 그래도 요즘 계속 생각하는 것은 "철학은 바뀌지 않는다"는 것이다. 데이터에서 정보로 이것이 지식으로 바뀌려면 얼마나 많은 고민을 해야 하는지 ? 회사에서 있었던 일이다. 현장에서 원소재 두께를 측정한 기록이 바인더로 7권이 존재했고, 데이터화 하는 작업이 알바 2명으로 7일 걸렸고, 정보화 작업이 직원 2명 2일 걸렸다. 지식으로 바꾸는데 일주일을 고생했다. 그런데 이번에 이런 일을 하면서 한번 더 고민해 보게 된것이 있다. 그것이 뭐냐 하면 지식화 되려면..
오늘은 회사 출근해서 뭘 해야 할까 고민을 하다가 시작한 것이 있다. 제가 관리하는 서류중 3정 5S 체크리스트가 있다. 오늘은 그것을 개선해 보기로 마음을 먹었다. 요지는 이렇다. 과거에는 현장을 둘러볼때 사진기와 관찰자만이 필요했다. 그리고 현장에서 개선되어야 할 사항만을 찍어, 개선 보고서를 작성했다. 서류는 양식화 되어 있었지만... 그런데 이상하게 내 눈에는 보이는데 직원들 눈에는 안보이는 것이다. 고민을 했다. 결국 답을 찾았다. 아는 것과 모르는 것에서 결과가 나온다는 것을 그래서 체크리스트를 현장에 가지고 다니면서 확인 할 수 있도록 바꾸었다. 어떤식이냐? 예를 들면 과거에는 " 원소재관리상태 : 양호" 이런식으로 현장을 둘러 보고 온 후 적는다. 이것을 이렇게 바꾸었다. 원소재의 보관 상..
1. 업무 범위 - 국세청 심청 세무 감사에서 벗어 나기위한 고철 관리 방안. - 원자재 출고 금액 평균: 50 ~ 70 억원 - 월 발생 고철 금액: 1억원 - 원자재 투입과 제품생산간의 수율: 65 % - 세금 폭탄에 대한 사전 준비 (음 여기에서 국세청이 참 더럽다는 생각 함) - 감사기간( 1달 ) + 개선기간 ( 1달 ) 2. 문제점 - 생산 공장의 협소로 인한 절단 공정의 외주 처리 - 외주 처리에 따른 고철의 처분 방식 문제 발생 - 고철의 비용과 가공비의 차이를 차감하는 방식 채택 - 국세청 입장에서의 매입누락, 거래업체 매출 누락의 경우가 발생할 수 있음 - 고철의 발생량을 정확히 판단되지 않음으로 인한 생산수율의 정확한 판단 부재 - 고철 판매 방식에 따른 영업외 수익의 가감 발생 3...
1. 업무 범위 - 현장 작업 실적 입력 시스템의 목적과 미래 방향 - 설치대수: 50 여대 - 작업기간: 자료 작성 2일, 발표 1일 2. 문제점 - 자료의 증가로 인한 현장 입력이 늦어짐 3. 파생되는 문제점 - 업무 전산화에 관한 반항심 증가 - 간단한 문제임에도 확대 해석하여 전체 문제인양 표현 4. 각 분야별 개선 도출 - 프로그램적 시스템 속도 개선 - Network적 시스템 속도 개선 - 입력 단말의 고장율 감소 개선 - 메인 서버의 문제점 개선 - 현장과 전산실과의 대화 개선 (정기 조례 시간을 활용한 교육) 5. 작업후 결과 - 작업자 들이 현장 정보 입력을 왜 해야 하는지 이유를 알고 있다. - 눈에 보이지 않는 작업이 있다는 것을 사용자가 알 수 있게 하였다. - 어렵지만 해야 한다는..
1. 업무 범위 1) 월 평균 구매 금액 60억원 2) 평균 재고 금액 750억원 3) 개선 기간 : 6개월 (업무 개선 및 재고 조사 등등 ...) 2. 문제점 1) 청구 직원의 감에 의존한 발주 방식 개선 2) 악성 재고의 증가로 인한 재고 회전율 감소 3) 수주 납기는 단납기며 자재 조달 기간은 오래 걸림 3. 파생되는 문제점 1) 자재 출고 (사용량)중심의 청구 형태를 유지 함으로서 소재 사용이 Project에 따라 소요량이 달라짐을 반영하지 못함 2) 실재로 필요한 자재는 없는 경우가 발생 3) 자재가 없는 경우 대체재를 사용함으로 써 재료비 효율성이 떨어짐 4) 150억원의 재고 금액이 1년 이상 방치 5) 자재 관리 직원의 재고 관리 문제점 발생 6) 장기 적재에 따른 자재의 보관 상태 (제..

5년에 걸친 원재료의 개선을 효과를 그래프로 나타낸 실적이다. 비정상 출고의 금액은 124억 에서 26억으로 줄었으며, 출고의 신뢰율은 81%에서 96%로 변경되었다. 재고의 정합성은 90%에서 97%로 변경되었다. 중요한 것은 2008년에서 2009년으로 넘어간 부분인데, 현장에서는 개선을 실시하였으나 숫치상 잘못된 경영을 한 것으로 보인다. 그러나 이 부분은 과거에 잘못관리된 부분을 개선함으로 나타나는 일시적인 현상으로 이를 경영자가 직원을 믿지 못하고 직원을 채근하게 되면 직원은 변화를 힘들어 하게 된다. 중요한 것은 경영자가 직원을 믿어주고 끝까지 올바른 방향으로 개선 되도록 지도하고 이끌어 줘야 한다는 것이다. 한 가지 더 "너무 단기적 성과에 연연하면 장기적 성과를 거두기 힘들다. "
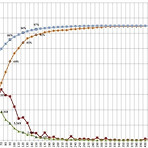
개선를 진행하면서 항상 생각되는 문구가 있다. "초우량 기업은 평범한 기업이 하지 않는 일을 하는 것이 아니라 평범한 기업들도 하고 있는 일을 탁월하게 하는 것이다. " 상기 내용은 수주를 하고 제조카드를 투입하는데 걸리는 시간을 나타낸 자료이다. 갈수록 심각해 지는 수주 활동에서 고객은 납기 단축, 높은 품질, 낮은 가격을 요구해 오고 있다. 하지만 우리가 하는일이 고객을 만족하기 위해서 노력을 하는 것인지 ? 수주 승인후 제조카드의 투입까지 걸리는 일자의 47%는 한달 (30일)이 지나도 투입이 안된다. 기본을 너무나 모르고 있었던 것이 아닐까 생각한다. 모든 일은 시작이 중요하다. 시작을 해야만 마지막도 존재하는 것이다. 마지막은 항상 시작의 후순위에 있다. 이점을 잊지 않는다면 얼마나 많은 생산성..